Drum twister MWR
SKET Verseilmaschinenbau GmbH in Magdeburg supplies a wide range of machinery and equipment for the manufacture of cable and steel wire rope. “DRUM TWISTERS” play a significant role in the production of cable and occupy a resultantly important position in the SKET supply programme. With Drum Twisters from their MWR range, SKET offers stranding lines of great product specific flexibility and proven reliability for a wide range of applications.
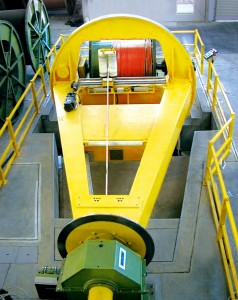
SKET Verseilmaschinenbau GmbH in Magdeburg has an extensive range of machines and equipment for the manufacture of cables and steel wire ropes.
The so-called "DRUM TWISTER" plays an important role in cable production and is therefore also an important part of the SKET delivery programme.
With the universal stranding machines of the MWR series, SKET offers stranding lines with high product-specific variability and convincing reliability for a wide range of applications.
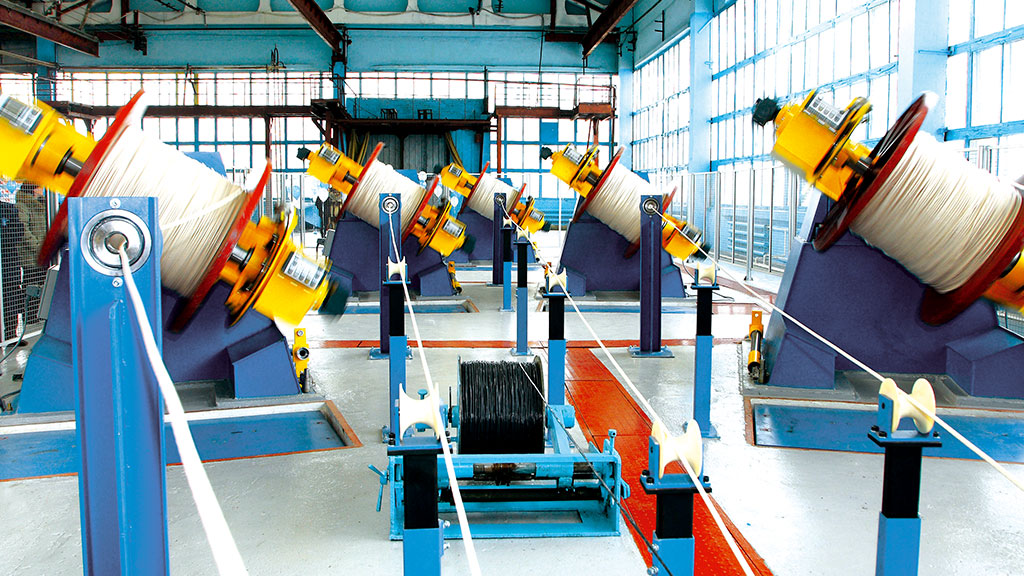
These machine systems embody experience and know-how for
- the manufacture of energy cables from round and sector conductors
- cable screening
- the armouring of cables with round and flat wires
- the manufacture of Milliken cable
- the production of bundle construction telephone cable.
Principle of Operation
Rotating pay-offs, sector guides with automatic correction, tape applicators, rotating belt haul-offs and rotating take-ups are all standard assemblies for the MWR range.
SKET Drum Twisters, which can be tailored to specific applicational requirements, offer the maximum of output efficiency.
Machine Arrangement
- Rotating Pay-offs,
with variable back-twist, drums having a flange diameter of 1250 to 5000 mm and a capacity of up to 50 tonnes, drums accommodated between pintles, horizontal and vertical arrangements and stationary and moving drum lifts for loading without the need for an overhead crane - Stationary Pay-offs,
for drums having a flange diameter of 1250 to 2240 mm and a capacity of up to 10 tonnes, driven, brake controlled and with drum-fill tension control - Sector Correction Equipment,
giving automatic positional correction for the sector shaped conductors during the stranding operation - Stranding Dies,
with quick-change lay-plate ( nipple and sector guides) for the rotating die, driven, free-rotating and stationary types - Tape Applicators,
for the application of plastic tapes, aluminium or copper foil, or steel tape
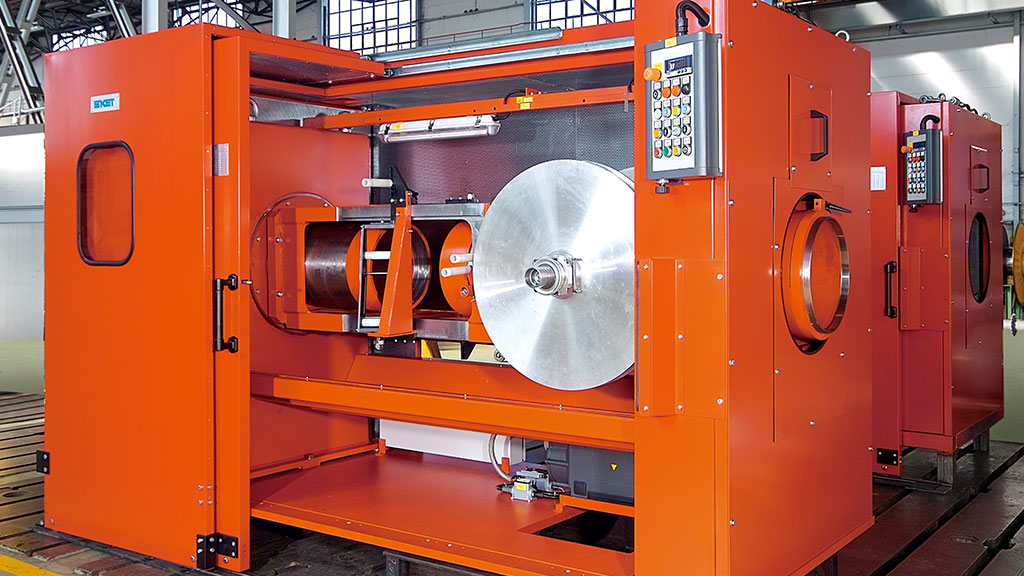
- Rotating Take-ups,
for drums having a flange diameter of 1250 to 5000 mm and a capacity of up to 50 tonnes, with drum accommodation between pintles and automatic cable travers-ing on the drum via a controlled drive - Rotating Belt Haul-offs,
having a pull of up to 6 tonnes and being available as a combination of two symmetrically arranged haul-offs, with separately controlled individual drives - Rotating Haul-off / Take-up Combinations,
as an alternative to individual assemblies, having the same technical characteristics as the separate assemblies and being of particularly space saving design - Ancillary Equipment,
depending on product specification and technology, the drum twisters can be complemented with the following assemblies:- pay-offs for fillers
- pay-offs for screening
- pay-offs for armouring
- pay-offs for longitudinal tapes
- pre-formers for armouring wires
Automation
- Individual assembly drives, choice of AC or DC technology
- Speed and angular alignment synchronization as well as torque and tension control
- Maintenance of product related quality parameters under all operating conditions via controlled machine stopping including in the event of a loss of the mains supply voltage (AC technology)
- Programmable control and operation via a touch-screen facilitate fully automatic process control, systems operation and monitoring, programme management, operating data storage, data recording, service functions and maintenance
- In-house electrical and electronic engineering and technology driven software development
Applications
The Manufacture of Energy Cables
Cable diameter | max. 200 mm |
No. of conductors | three, four or five, plastic insulated |
Conductor construction | single or multi-wire (Al or Cu) |
Conductor cross-section | 16 – 800 mm2 |
Shapes | round, straight sector shaped, pre-spiralled sector |
The Manufacture of Screened / Armoured Cables
Cable diameter | max. 200 mm |
No. of screening wires (copper) | max. 140 |
Wire diameter | approx. 0.8 – 2.0 mm |
No. of galvanized armouring wires | max. 120 |
wire diameter | approx. 1.6 – 4.5 mm |
No. of flat wires | max. 120 |
Dimensions | approx. 5×0.8 mm (width x height) |
The Manufacture of Milliken Cables
Cable diameter | max. 80 mm |
Conductor cross-section | 800 – 3000 mm2 |
Conductor construction | single or multi-wire (Al or Cu) |
Shapes | sector shaped pre-spiralled segmental copper conductors |
The Manufacture of Bundle Construction Telephone Cables
Cable diameter | max. 120 mm |
No. of main bundles | max. 24 |
No. of pairs | max. 4,800 |
Main bundle diameter | approx. 8 – 35 mm |
General Technical Information
Linear speed: max. 80m/min
Rotational speed in relation to production weight:
- 60 rpm up to 12 tonnes
- 50 rpm up to 15 tonnes
- 40 rpm up to 25 tonnes
- 30 rpm up to 50 tonnes