Planetary strander with back-twist MKVS
SKET MKVS Type Planetary Stranding Machines with Back-Twist are mainly used for the manufacture of high quality steel wire strand and ropes.
SKET Verseilmaschinenbau GmbH in Magdeburg has many years’ experience in the manufacture of complete production lines for the wire rope industry and offers wire rope manufacturers an extensive range of machinery and equipment for the stranding of steel wires and strand. Within the production programme, Series MKVS Planetary Stranding Machines occupy an important position. This range of planetary stranding machines with variable back-twist has been designed by SKET on the basis of extensive development work associated with drives technology, tension control systems and electronic regulation and control systems together with an understanding of the interdependence of the individual assemblies in a complete technological line.
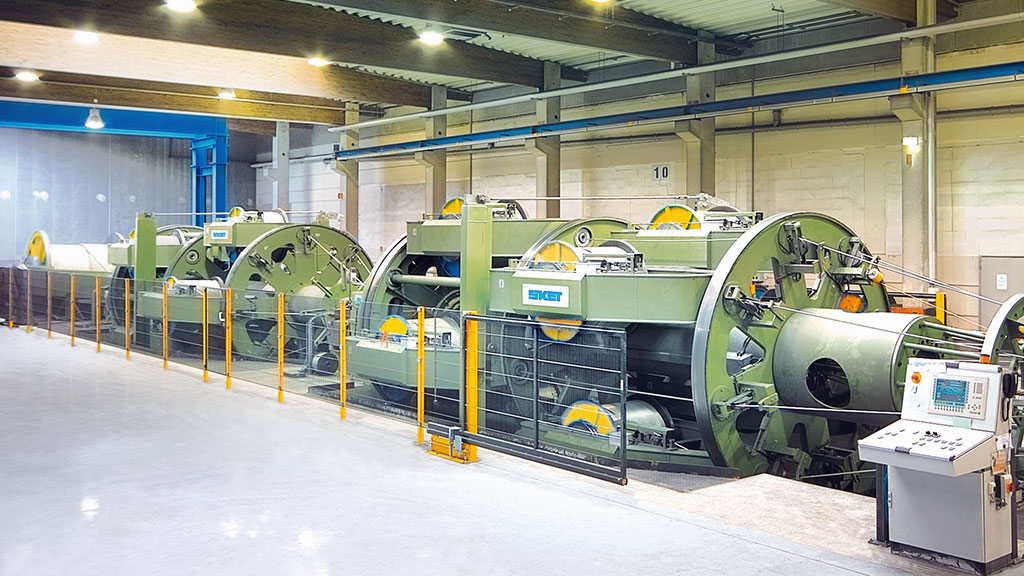
The SKET Verseilmaschinenbau GmbH MKVS machine system is of unit construction and, as such, can be built-up and shaped to meet the differing specific needs of users based on a basic machine concept. Continually increasing rope maker led demands related to quality, flexibility, productivity and automation mean that the machine and its main component assemblies are subject to continuous further development.
In order to meet increasing market demands, SKET has specialised, amongst others, in developing and manufacturing large-size planetary stranders for making long heavy-duty steel ropes.
Application Areas
- Manufacture of round and profiled strand out of high-tensile steel wires
- Manufacture of ropes from round and profiled strands including heavy-duty offshore and non-rotating ropes
- Manufacture of compacted ropes
- Manufacture of half and fully locked coil ropes
- Manufacture of umbilicals
- Armouring of PTFE tubes with steel wire (conduits)
Machine Description
State of the art stranding cage technology
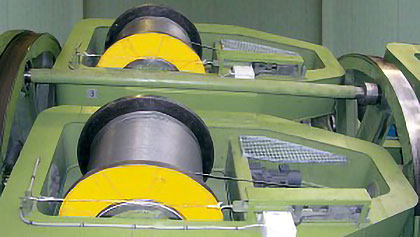
The stranding cages are, up to certain bobbin sizes or numbers of bobbins, of compact design and carried in encircling bearing style drive and bearing housings. The results are high speeds, low power losses and simplified machine maintenance. Larger stranding cages are supported by heavy duty underroller bearings. Cages are suitable to accommodate bobbins with flange diameters ranging from 315 to 2800 mm and weighing 40 tonnes max. The bobbin braking systems are designed to meet the particular requirements of the application. Different systems available offer simple measurement and indication of the back tension in the wire or strand, adjustment of the tensions by the operator from the machine control desk and automatic tension control.
State of the art drives technology
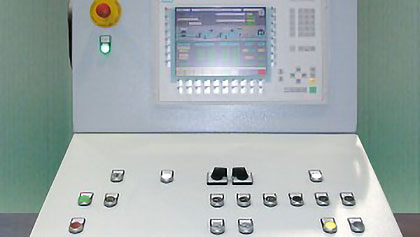
Separate drives to the stranding cage and the haul-off enable a very wide range of lay-lengths to be covered. Using modern digital control technology, infinitely variable and reproducible lay-lengths can be set from the control desk. The back-twist drive makes variable back-twist possible within a 65 to 135% range.The use of special speed modulation gearboxes enables high back-twist moments to be transmitted.Differing degrees of back-twist are possible within a single cage. Different cages within a machine can be infinitely variably controlled in relation to each other.
A special loading drive enables the cage to be rotated into place and stopped in each loading position.
State of the art machine sub-assemblies and auxiliary equipment
Technology essential for a high-performance stranding machine includes:
- modern pay-off and take-up solutions offering stationary, rotating and traversing technology and, where required, the possibility to reverse, suitable for reels with flange diameters of up to 6000 mm and a maximum width of 10,000 mm weighing up to 600 tonnes
- optimum single capstan and double capstan haul-off technology matched to the requirement, featuring capstan diameters of up to 5000 mm and a maximum haul-off pull of 800 kN
- special pre- and post-formers to ensure optimum treatment of the stranded or finished product
- special calibration and compacting equipment, and lubricating systems
State of the art automation
- separate machine assembly drives using controlled DC or AC technology
- synchronisation of speed and angular displacement and torque and tension control
- maintenance of product related quality parameters under all conditions of operation with controlled machine stopping in the event of a loss of supply voltage (AC technology)
- the use of programmable controls in conjunction with touch screen operation makes possible fully automatic process control, operation and monitoring, programme management, data collection, record keeping, service functions and maintenance
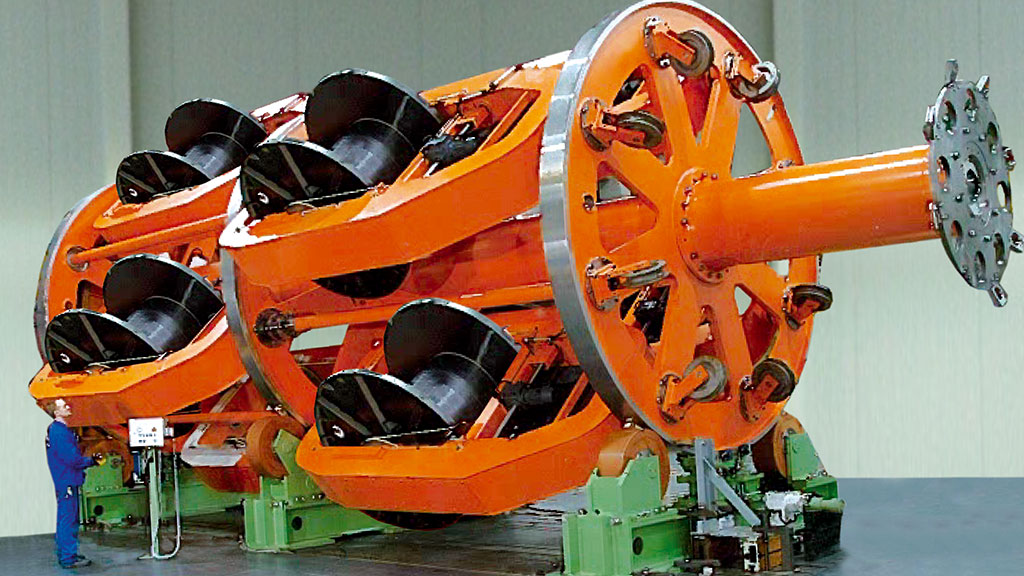